When National Raisin Company realized they needed to streamline their coding and marking process across their entire manufacturing plant, they reached out to REA JET to collaborate on a solution.
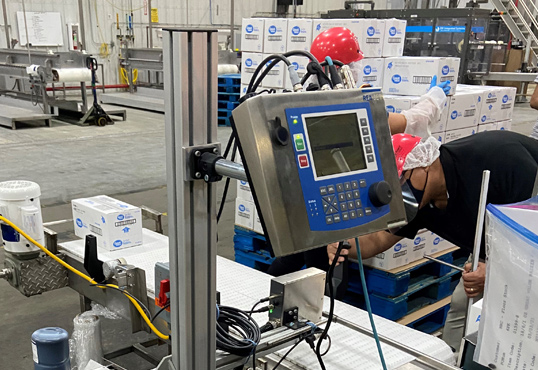
The latest generation of REA JET GK 2.0 high resolution coding and marking systems using piezo technology is suitable for direct, high-contrast coding and marking on absorbent and porous surfaces, such as cardboard, wood, and paper, with a variable print height of up to 100 mm.
About National Raisin Company
Since being founded in 1969, National Raisin Company has made its mark as the largest independent grower, processor, and packer of dried fruits in the United States. The unequivocal leader in private label dried fruit production, National Raisin, serves various customers within the retail, industrial, and food-service sectors, providing both conventional and organic products. In addition to dried fruit, National Raisin’s facilities also contain:
- A state-of-the-art research and development laboratory
- An assemblage of advanced packaging machinery
- A vibrant, passionate workforce
▼ Challenge
National Raisin's main challenge was that all of their boxes were being printed, folded and flat, in a central location before making it to the actual packaging line. This then required National Raisin to know ahead of time exactly how many packages needed to be printed.
If they printed too few boxes, they would have to stop packing and wait on more. If they printed too many, there were additional boxes left after the production run. Saving inventory space, reducing unnecessary labor and avoiding dreaded downtime became National Raisin’s main goal.
Recognizing an opportunity, the Packaging Manager at National Raisin, Tim Ramirez, reached out to REA JET and began discussing solutions with Account Manager Richard Hultberg.
“Before implementing REA JET technology, we were running through about 25 to 30,000 cases in our production facility that needed to be pre-printed in an area off to the side of our main production facility. That process required two shifts and somewhere between three, sometimes four people."
"So there were two objectives, one was to reduce labor, but the second was to get more control and streamline our inventory because we had cases sitting in storage as intermediate printed inventory. There’s a lot of admin support to reconcile that inventory regularly. It would be better to take clean blank boxes to the line for printing in real-time.”
Tim Ramirez, Packaging Manager, National Raisin
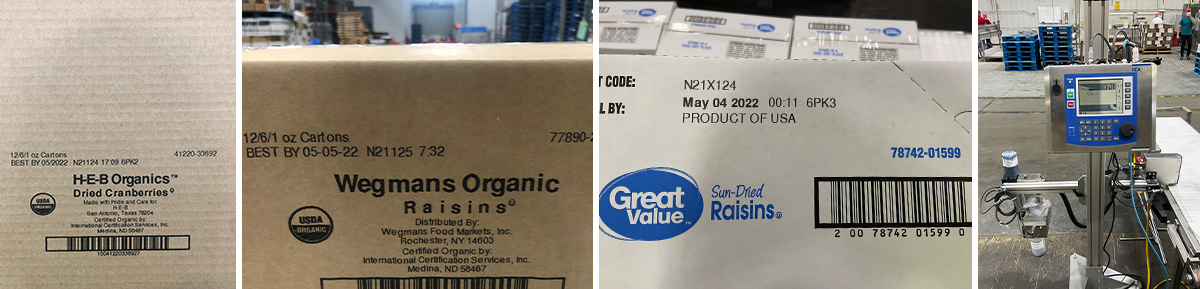
Text, 1D/2D codes and images such as company logos or product images can be combined freely. A horizontal resolution of up to 1200 dpi ensures high print quality with excellent edge definition directly on the product. The next generation of Piezo inkjet printers is thus a cost-saving and flexible alternative to labels or pre-printed boxes.
▼ Solution
Richard Hultberg understood the pain points and recommended integrating the REA JET GK 2.0 High Resolution printer directly onto the packaging line. This allowed all packaging to be printed in real time, eliminating inventory miscalculations.
After evaluating the existing operations at National Raisin Company, the comparison in cost per print with REA JET inkjet technology was about equal to their current process. However, after demonstrating reductions in operational costs and the benefits of the ability to control the printers remotely, the decision was made to go with the REA JET and the GK 2.0 High Resolution Inkjet Printer.
"After the initial sale, we ran into some roadblocks with adoption from the operators on the line running two shifts a day across multiple production lines. New line operators would have to interface with our equipment with little to no previous experience using it."
"We helped alleviate this issue by connecting the new printers to their network and allowing them to access the controllers remotely. In addition, we provided training and onsite technical support from day one of the partnership."
Richard Hultberg, Account Manager, REA JET US
The support provided on the initial two production lines built National Raisin’s confidence, and they implemented the REA JET solution to all their production lines.
▼ Results
Because REA JET was able to provide a single coding and marking solution that replaced two inefficient printing technologies, National Raisin Company was able to cut their overall costs in half.
Through our combined efforts, National Raisin and REA JET modernized printing on their packaging to boost operational efficiency, increase reliability, and reduce production costs.
"Incorporating REA JET here at the plant has saved a lot of money, not only in labor but also in unnecessary intermediate inventory print errors that we were having with the former system used in our print shop."
"Another good thing about REA JET is that they’re always available. I can call Richard, or I can call Antonio – the technical service is reliable and responsive."
Tim Ramirez, Packaging Manager, National Raisin
The right technology for your coding and marking needs
Contact REA JET
- Call Us: 440-232-0555
- Email Us: sales@reajetus.com